Reasons one to five: Simple fast and reproducible alignments
LMK Position – Robotic Luminance Camera System
Alignment and measurement with 6-axis robot
LMK Position is a robotic measurement system that combines a high-resolution LMK luminance camera with a 6-axis industrial robot. It offers automated, precise and reproducible measurements for all types of displays and is particularly suitable for automotive applications.
The system simplifies and accelerates the entire measurement process:
- Automated alignment: time-saving, low-error, reproducible.
- Flexible measurement: In accordance with international specifications and standards (e.g. DFF, ICDM) (external links) and can be combined with various measuring devices.
Thanks to intelligent image processing and proven calibration technologies, LMK Position is the ideal solution for research, development and small series production.
Top ten reasons for LMK Position
- Fast vertical alignment: Automated DFF-BlackMURA alignment in just a few seconds
- Precise angular measurement: Fully automated and highly accurate goniometric measurements.
- Exact conoscopy: Automatic alignment of our conoscope on any free-form display using 3D scan including pixel structure avoidance.
- Full range of movement: 6-axis movement without restriction thanks to secure cable routing.
- Intelligent tripod: Multiple storable camera positions for consistent reproducibility.
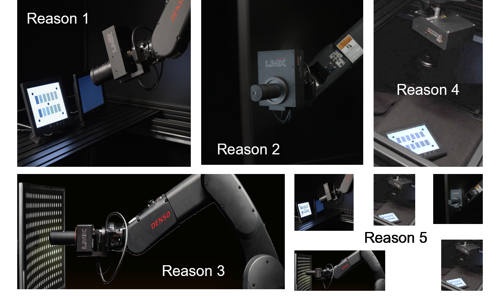
- Easy handling: No need for complex, one-off fixings - ideal for prototypes.
- More detail thanks to image fusion: Higher resolution thanks to image stitching - depending on the lens.
- Intelligent functions: Automatic focus, defocus, sparkle-scan and virtual image distance measurement - even with manual or fixed focus lenses.
- Multisystem compatibility: All alignment functions can also be used with spectroradiometer specbos 1211 & specbos 2501.
- Modular and flexible: Luminance camera, spectroradiometer and robots can also be used individually - with temporary system dismantling.
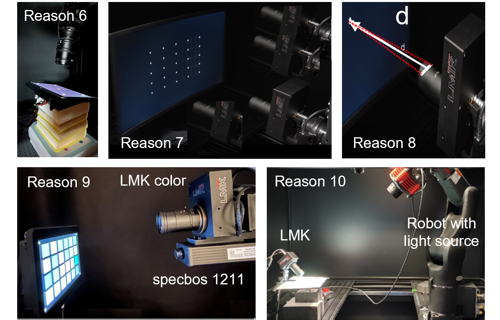
Reasons six to ten: Cost efficient and future proof metrology improvements
REQUEST MORE INFORMATION NOW AND ARRANGE A DEMO!
Integration & Security
TechnoTeam offers complete integration on site in the EU, South Korea and China. All relevant security standards are met. Documents on the installation and scientific publications are available here.
Technical data | |
---|---|
Maximum arm reach | 875 mm |
Number of axis | 6 |
Position detection and motors | Absolute encoder; AC servomotors and brakes for all joints |
Motion range | J1: +/-170°; J2: +135° -100°; J3: +153° -136°; J4: +/-270°; J5: +/- 120°; J6: +/-360° |
Position repretability (at the center of the camera mounting) | +/-0.03 mm |
Weight with Alu profile rack (incl. robot, LMK, controller, cables) | <150 kg |
Alu profile rack dimensions (L × W × H) | 780 × 780 × 950 mm (Robot installation height: 970 mm) |
Compatible cameras | LMK5, LMK6-5, LMK6-12, LMK6-30 |
Installation environment of robot | Temperature: 0 to 40°C; Humidity: 20 to 90% RH; Vibration:4.9 m/s² (0.5 G) |
Optional equipment | 7th axis (linear) mounted below the robot (below J1) Specbos 1211-LAN VIS-NIR spectroradiometer, Industrial operation PC (19'' rack) |
RELEVANT PRODUCTS AND APPLICATIONS
Publications
International Conference on Display Technology (ICDT 2021)
SID Vehicle Displays & Interfaces 2022
Journal of the Society for Information Display
SID Vehicle Displays & Interfaces 2021
- Type:
- Package
- Applications:
- Automotive Display
- Measurands:
- Color measurement Light measurement
- Tasks:
- Automation & Industry Development & Industry Science & Research